The AgBOT Competition
To create a full-scale autonomous vehicle to navigate, fertilize, identify and eradicate weeds in an agricultural field
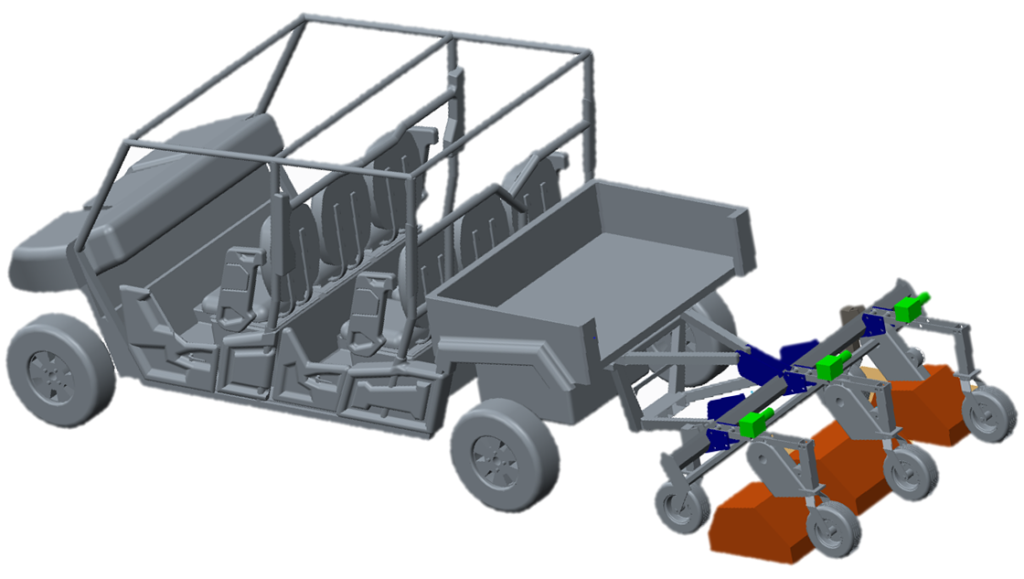
Top-down skeleton modeling
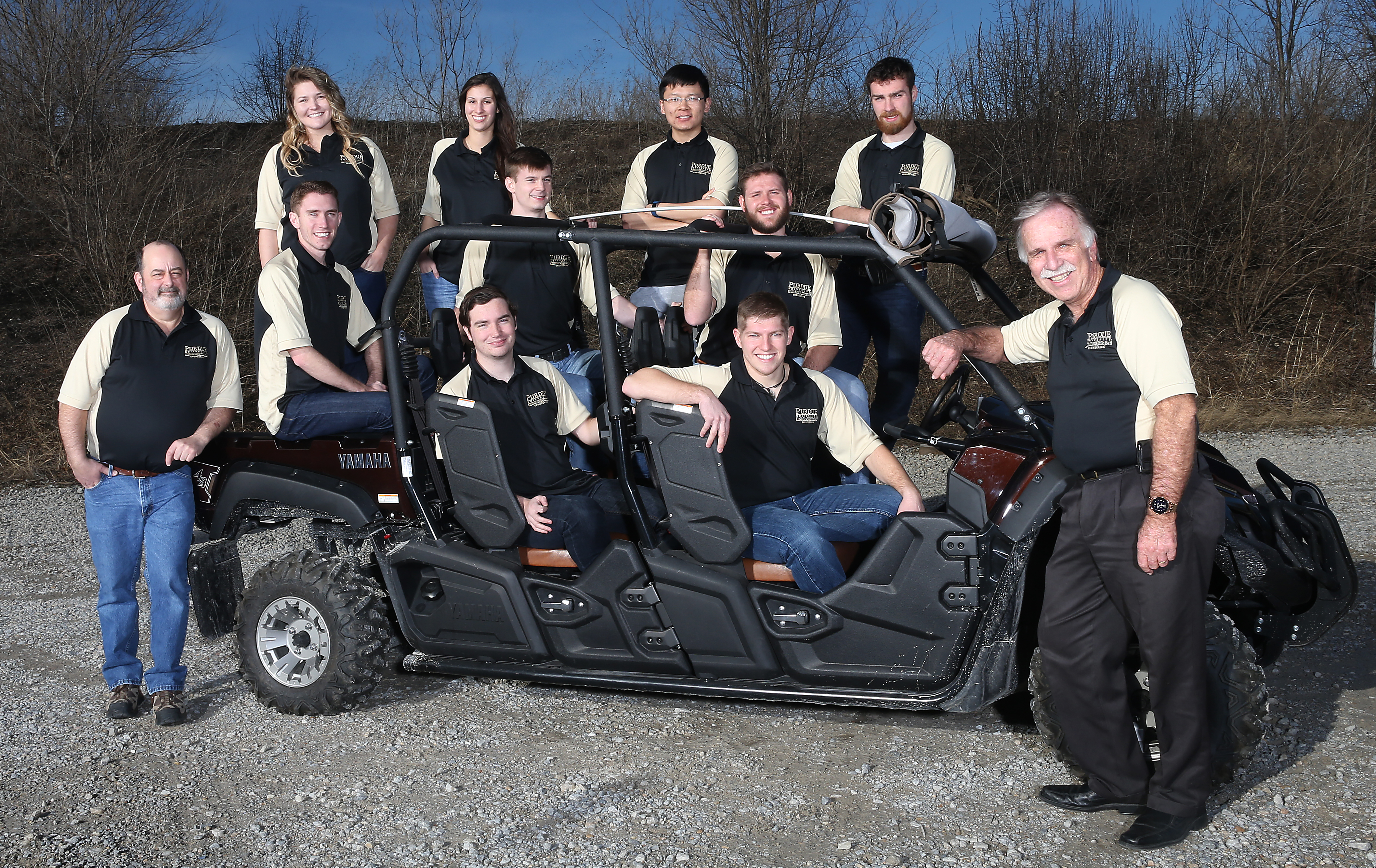
The AgBot Challenge
The project requires the simultaneous integration of automating 6 unique operations
- Power System
- Vehicle Navigation
- Chemical sprayer
- Crop Pesticides (3 different types)
- Crop Fertilizer (1 type)
- Physical weed eradication
- Multivator blades
- Weed Identification
- Centralized controller
Purdue’s AgBOT: Our Solution
Our robot is projected to autonomously:
- Identify and locate 3 common types of weeds and corn plant
- Physically eradicate all weeds outside the lines of crop
- Apply pesticide to weeds with the correct pesticide (3 types)
- Apply fertilizer to corn crops
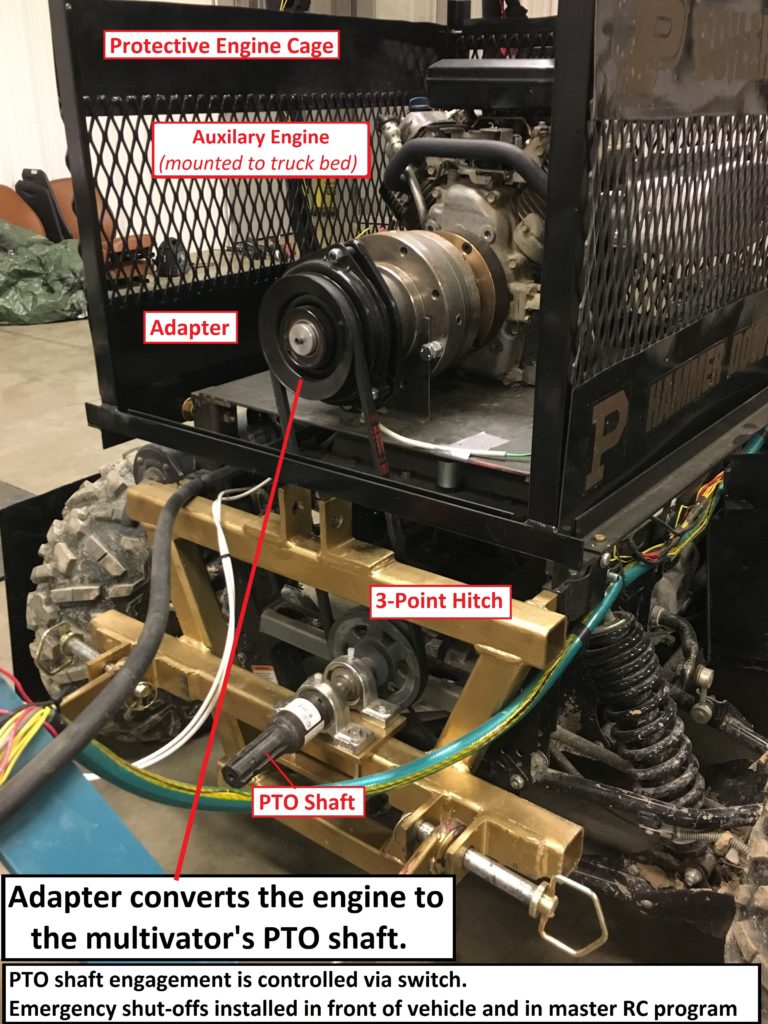
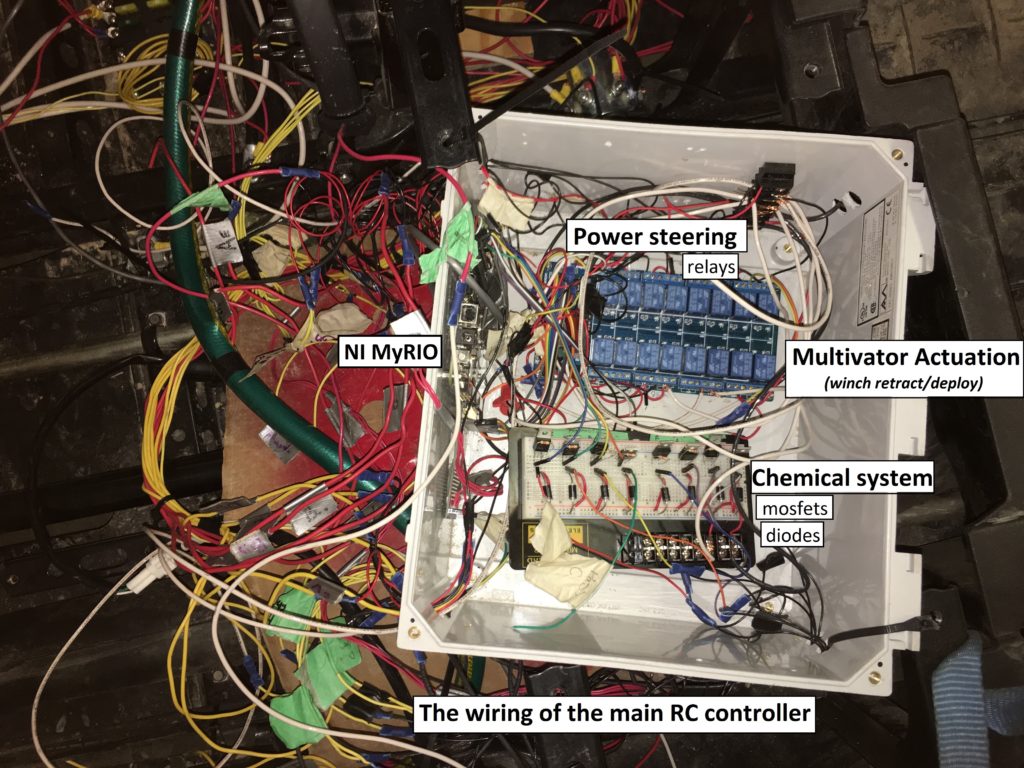
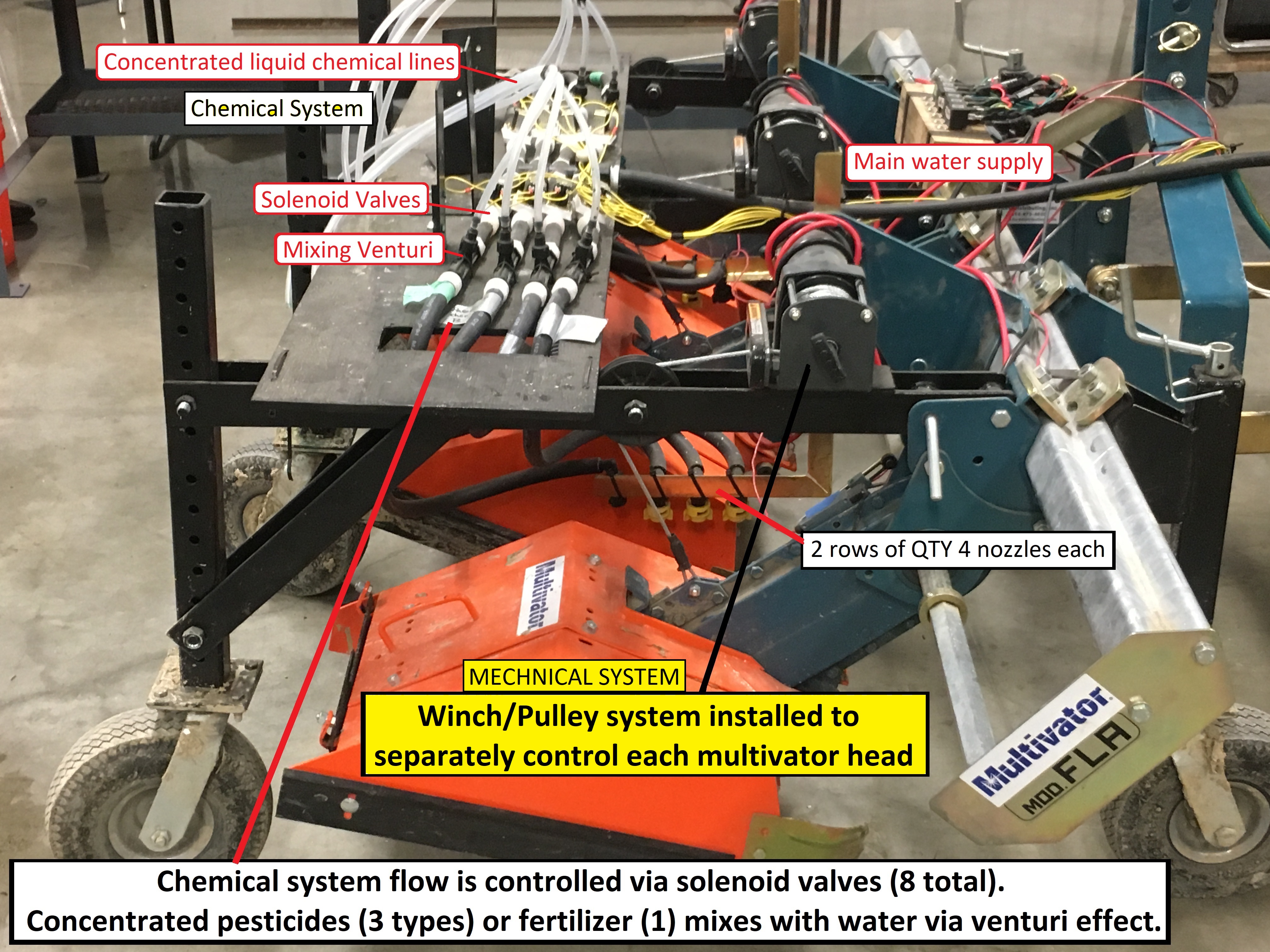
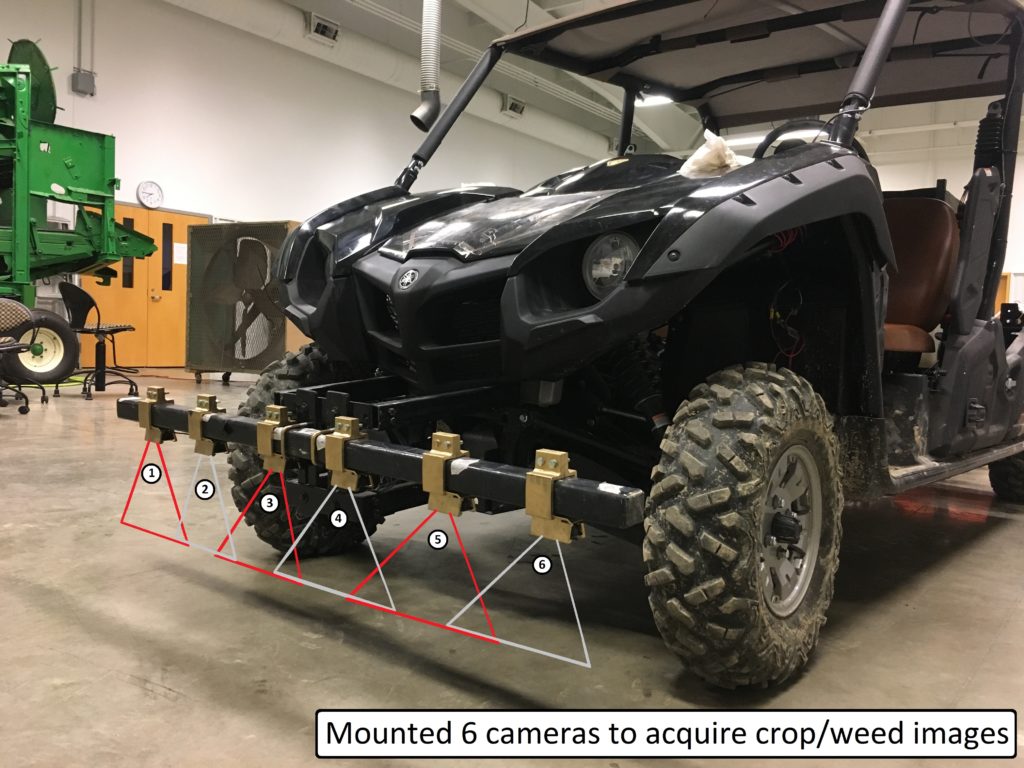
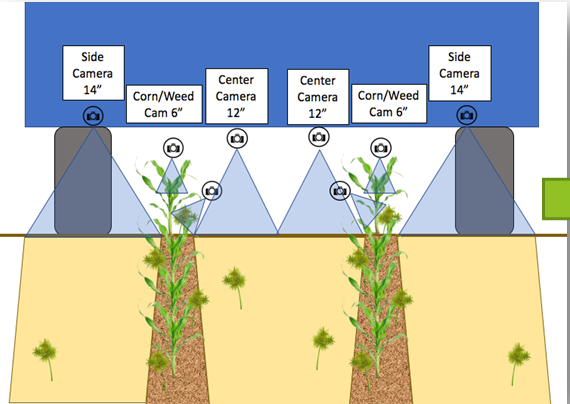
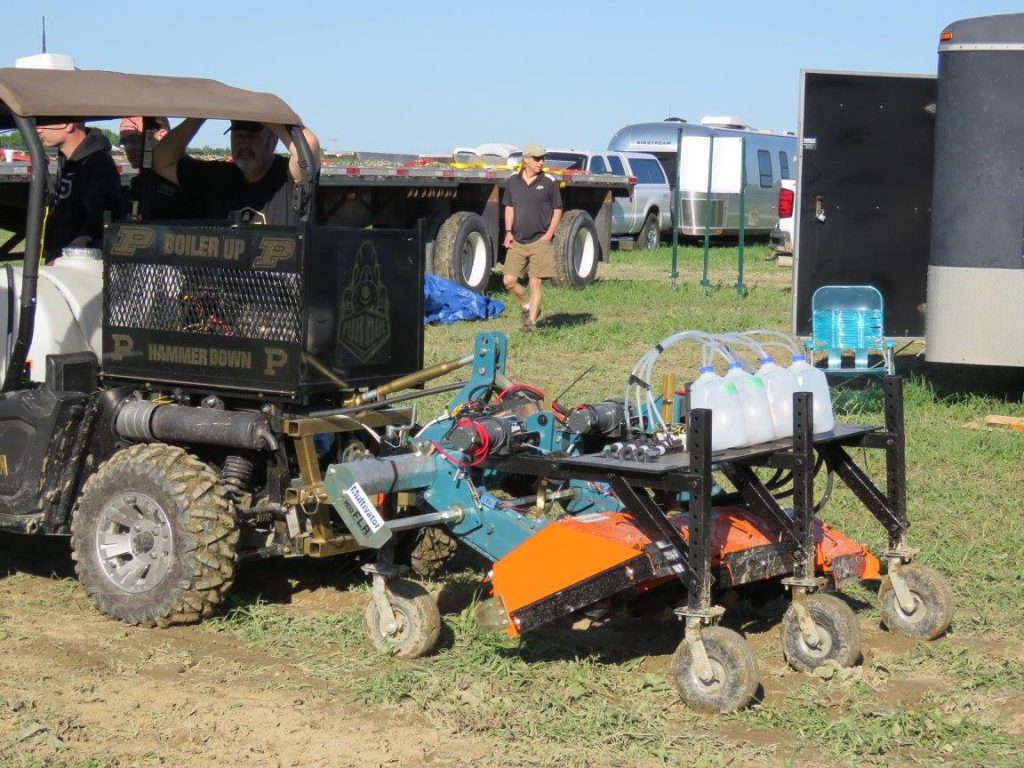
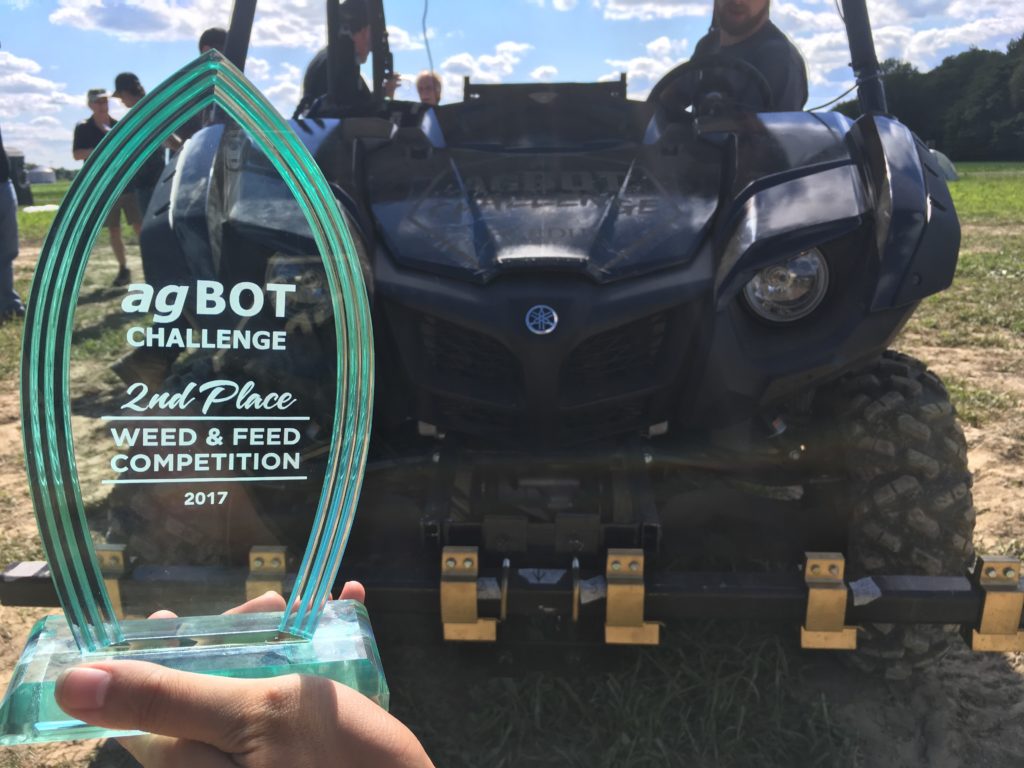
Miscellaneous Project Information
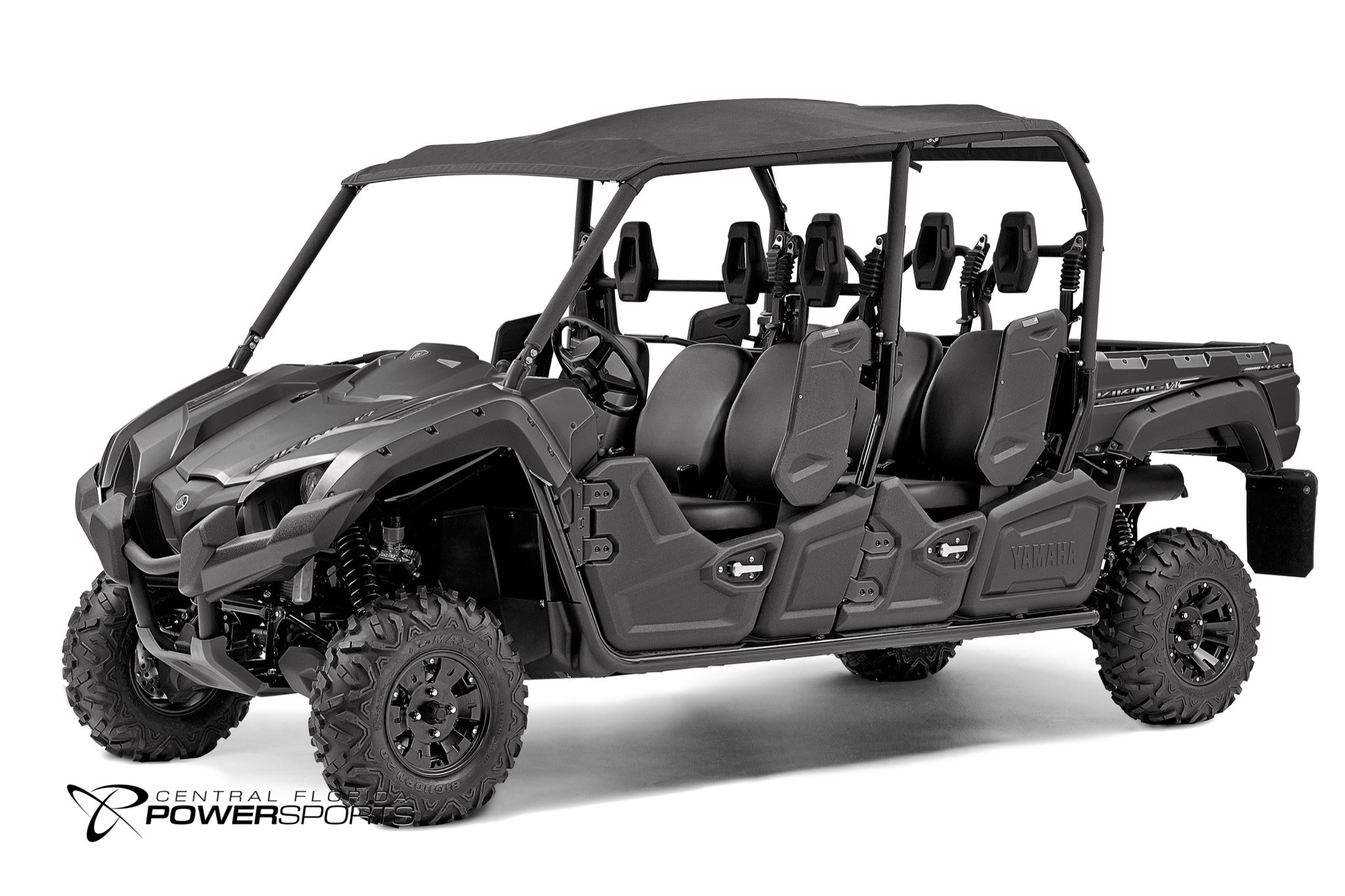
The 2016 Yamaha Viking VI EPS, Ranch Edition
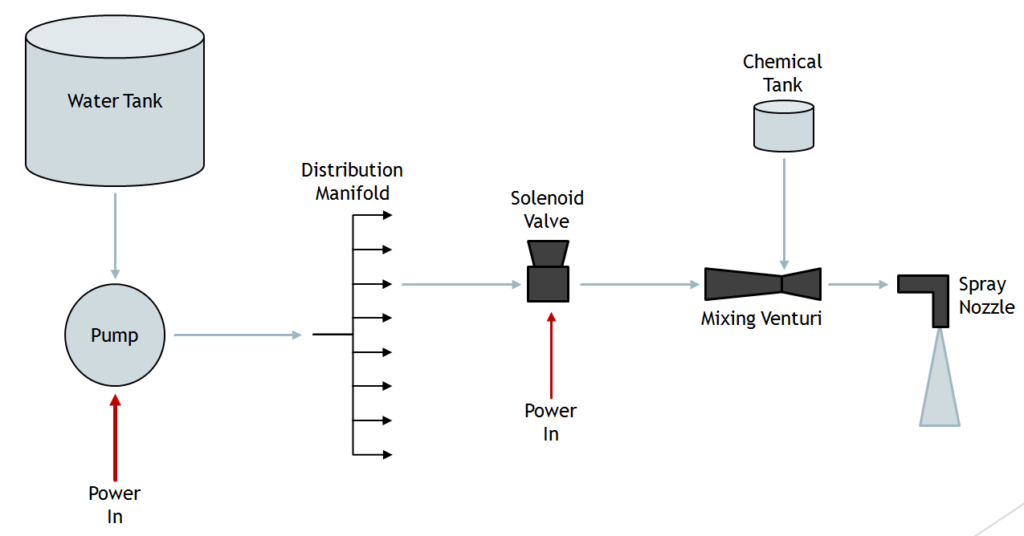
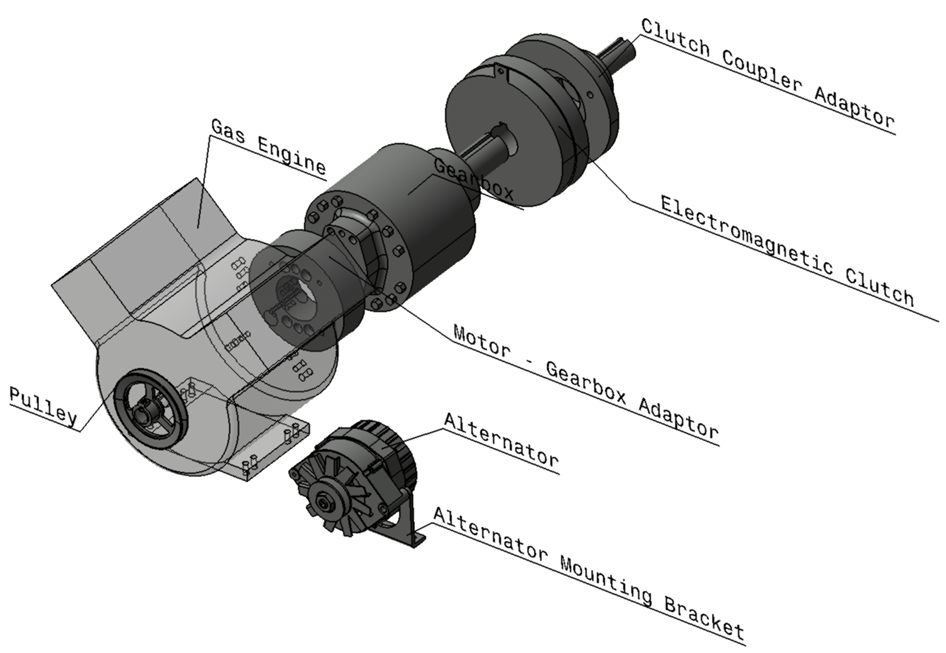
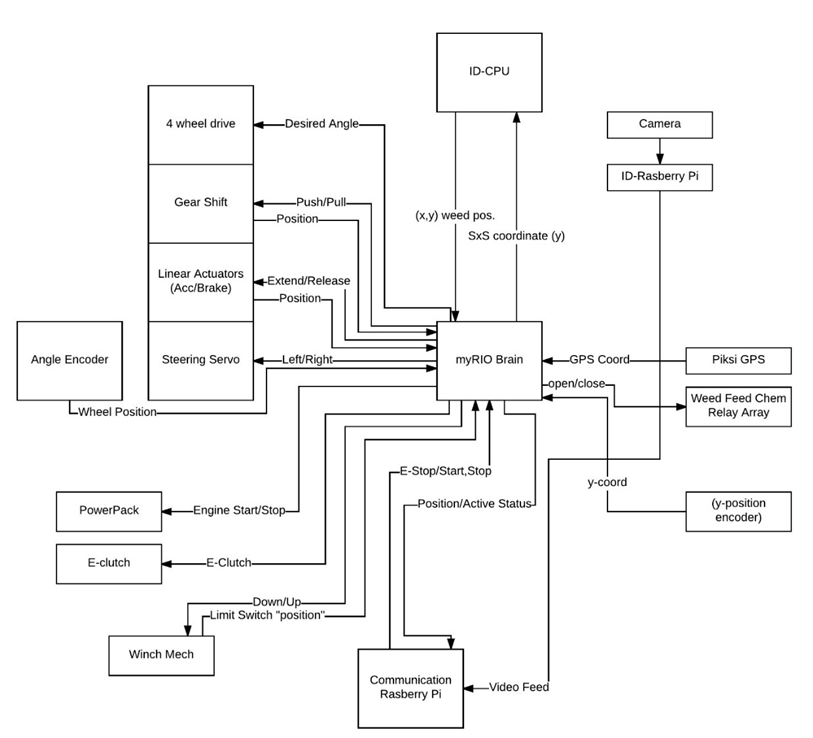
Our Design Overview
1. Power System
A spare engine was mounted to the bed of the Yamaha vehicle. A gearbox adapter was fabricated to convert the engine’s RPM to the correct RPM for the Multivator’s PTO shaft. The engine’s clutch could be activated via button, which would engage the the Multivator’s blades.
2. Vehicle Navigation
The Yamaha vehicle’s power steering was re-wired to allow for control via activation of relays. The relays were controllable via our central control system, and could be engaged autonomously.
3. Chemical Spray System
A large water tank was installed into the back of the Yamaha vehicle. A pump transported water to the back of the vehicle. Using 8 venturi mixers, concentrated pesticide or fertilizer mixed with the water line as it flowed towards one of 8 nozzles. Solenoid valves were controlled via MOSFETs, and were controllable via the centralized control system.
4. Physical Weed Eradication (Multivator)
Physical weed removal is achieved by utilizing the Multivator, a farm cultivator. Generously donated by Ford, our team mounted 3 winches to the infrastructure to control the actuation (deploy/retract) of each Multivator head via the press of a button. The power system, once engaged, would turn the blades for weed eradication.
5. Weed Identification
By means of integrating machine learning principles, the identification system was aimed at having the centralized controller automatically differentiate and identify between 3 types of weeds and corn crops. Using 6 Logitek cameras in the front of the vehicle as input, the identification system would reference an archive of weed/crop photos in different conditions to output the final plant identification autonomously.
6. Centralized Controller
All sub-systems on this AgBot robot were centrally controlled via the master central controller. This central controller consisted of a NI MyRio, a Raspberry Pi, and a Dell desktop computer, and were mounted in the back seats of the Yamaha vehicle.
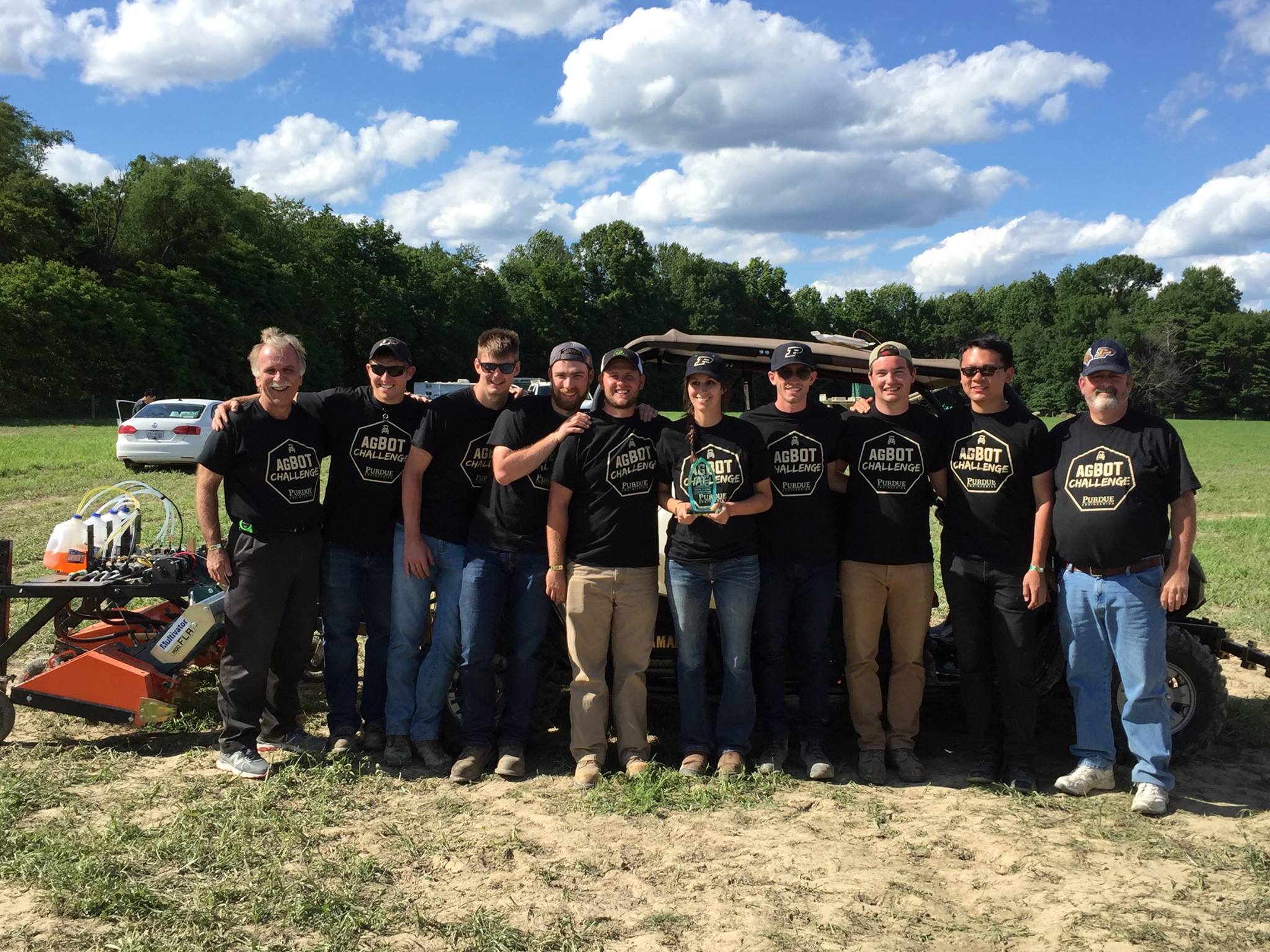